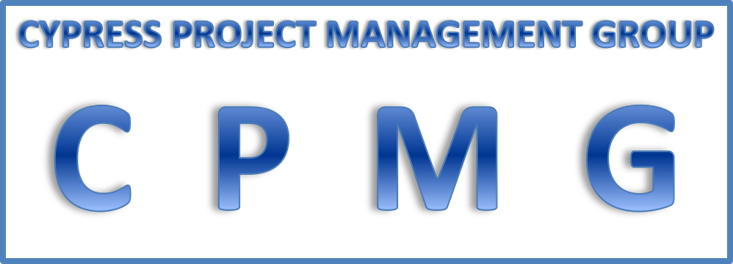
CPMG is a Minority Business Enterprise located in Longwood, Florida, USA (Orlando suburb). We are a Project Management Office (PMO) that specializes in project development & execution according to the global standards and methodologies of the Project Management Institute (PMI). Our focus is primarily heavy industrial, commercial, and government/municipal projects.
CPMG is composed of a core group of professionals with diverse qualifications equivalent to approximately 100 years of total experience. Our experienced project team will assist you with clearly defining project scopes, develop detailed project plans, and execute your project(s) on time and within budget. We are the preferred partner for municipalities and business owners (or Executives) to help them achieve the desired growth in their city or business. We are the solution for their staff deficiencies.
Successful projects require more than well-planned schedules or well-balanced budgets. They require skilled and motivated people. We provide management and technical services for turnkey projects, as well as integrating such services into specific sub-project scopes. We take concepts, define the scope of work to realize the final product/service, execute the scope in accordance with the scope definition and quality guidelines, and validate the product/service for our customers. Project managers regularly face tough decisions about where to concentrate project resources when met with competing priorities and demands. As your PMO, it’s our responsibility to identify and fulfill your project’s staffing needs. Project integration management helps with these decisions by ensuring the proper coordination of project processes during project plan development and execution.
We consider our services to be best-in-class, globally. We have implemented totaling more than $100 Million for clients. CPMG offers our clients and partners the support and services:
MANAGEMENT SERVICES
- Conformed Specification & Contract Management
- Quality Management & Source Inspection/Surveillance
- Risk Management
- Schedule Management
- Supplier/Vendor Management
- City Planning & Land Development
- Site Construction Management
- Regulatory Compliance & Management
- Merger & Acquisition Integration
INFORMATION TECHNOLOGY SERVICES
- Business Process Management Systems
- Production Management Systems
- Quality Management Systems
- Inventory Management Systems
- Safety & Security Systems
- Emergency Management Systems
OTHER TECHNICAL SERVICES
- Electro-Mechanical Products & Systems
- Equipment Maintenance & Overhaul
- Production & Test System & Automation
OUR BENEFITS
Following are benefits that our clients have realized over the several years as a result of our services. We expect any/all current or future clients to embrace similar benefits to meet their growth and performance expectations. Simply put, we DELIVER!
- Developed and executed Canadian Regulatory Compliance Plans for equipment design, manufacturing and construction. Managed all aspects of regulatory compliance for the project.
- Successfully executed the design, construction and/or commissioning of 3 new combined cycle power plants with a total value of approximately $600 million.
- Managed multiple domestic and international Fossil, CT, & Nuclear Power Plant turbine & generator refurbishment and/or upgrade projects with a value of $1.8 Million to $65 million, an new plant construction with a total value of $600 million. These projects consisted in the manufacturing, transportation and coordination of heavy industrial equipment and construction. Several projects were managed simultaneously. Projects were completed within designated budgets to achieve 26% to 44% profit margins.
- Created a land development plan and strategies for the Oldest Incorporated Black Municipality in the United States. Our plan would provide this town approximately $18 Million in revenues within 5 years of execution.
- Managed projects per associated contracts to meet contractual obligations, while mitigating or avoiding risks up to 20% of the contract value and negotiating additional sales of 10-15% of the original contract.
- Developed and implemented Supplier Chain Management System that defines roles and functionality of all users, established guidelines for approval and disapproval, and established performance metrics. System reduced incoming inspection by 75% while also improving supplier commitment.
- Developed & implemented software for Material Discrepancy Reporting System with security measures and functionality to include automatic notification, workflow control, standard root-causes, and automatic reporting based on operational performance metrics. Improvements increased efficiency of the system by 60%.
- Developed and implemented product design changes to aid in manufacturability of products which in turn yielded $500,000 annual cost reductions while also improving production throughput yield by 30%.
- Developed strategies and implemented design improvements for products with high failure rates through standardization methods. Results yielded 90% reduction in first-time quality issues and over $5.5 million in annual cost reductions for product.
- Developed and implemented automated test equipment, including packaging and software that contained safety features, data processing, and quality control. Improved rejection of poor-quality parts by 70%.